De bedste metoder til en grundig årsagsanalyse
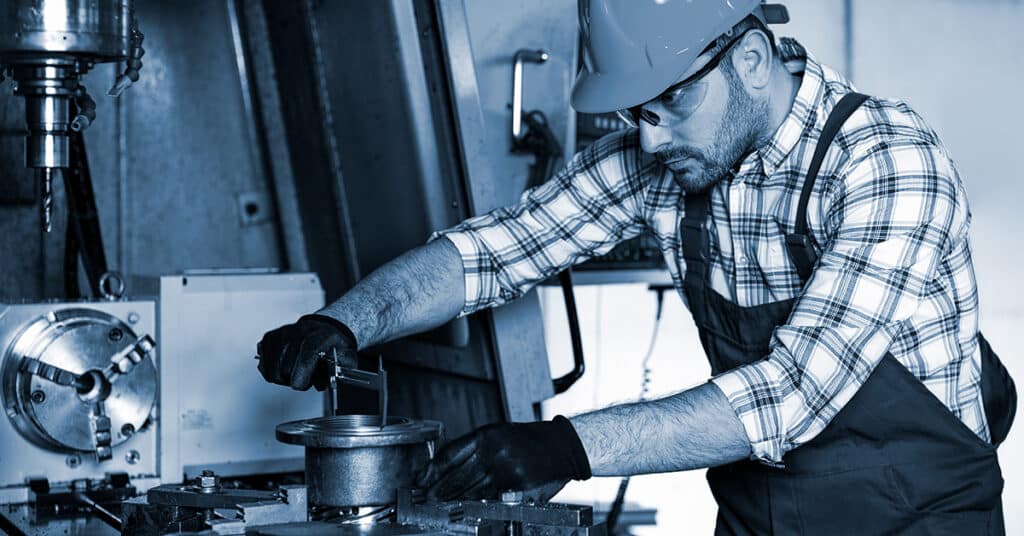
Årsagsanalyse er en metode til at identificere og løse problemer i tekniske processer. Denne tilgang er særligt effektiv, da den fokuserer på at fjerne den underliggende årsag til fejlen permanent, frem for blot at adressere de symptomer, som fejlen medfører. Metoden kan med fordel indgå som en central del af en vedligeholdelsesstrategi, da den bidrager til at forebygge gentagne fejl og optimere driftssikkerheden.
Årsagsanalyse anvendes ikke kun til tekniske udfordringer, men kan også afdække processer, rutiner, mangler eller andre faktorer, der bidrager til problemerne.
Ved at identificere og eliminere den egentlige årsag kan virksomheder forbedre deres indtjening, især i brancher med produktionskritisk udstyr. I dette blogindlæg vil vi derfor gennemgå, hvordan du kan arbejde med årsagsanalyse for at opnå en mere stabil produktion og minimere unødvendig nedetid.
Problemet
En virksomhed i stålindustrien stod overfor betydelige problemer med en maskine, der ikke transporterede glas jævnt. Ingen kunne forstå årsagen, og som en midlertidig løsning rengjorde operatørerne maskinen flere gange om dagen for at håndtere symptomerne.
Til sidst valgte vedligeholdelseschefen at iværksætte en årsagsanalyse for at finde en permanent løsning på problemet. Projektgruppen begyndte analysen med metoden „5 gange hvorfor‟ for at afdække den underliggende årsag.
Metoden „5 gange hvorfor‟
„5 gange hvorfor‟ er en enkel, men effektiv metode til at finde årsager ved at stille spørgsmålet „hvorfor‟ fem gange i træk. Denne spørgeteknik stammer oprindeligt fra Toyota, hvor den spillede en central rolle i at skabe store forbedringer for bilproducenten.
Metoden fungerer på den måde, at svaret på det første „hvorfor‟ danner grundlaget for det næste spørgsmål. Processen fortsætter, indtil den egentlige årsag er identificeret, og den kan adskilles fra symptomerne.
I dette tilfælde blev svarene på de fem spørgsmål således:
Problem: Maskinen kan ikke transportere glas jævnt.
- Hvorfor? Der opstår brodannelse i genopfyldningsbeholderen.
- Hvorfor? Fordi den automatiske fluidisering ikke fungerer.
- Hvorfor? Fordi signalslangen har en lækage.
- Hvorfor? Fordi varme savegnister har brændt huller i den.
- Hvorfor? Signalrøret er udsat og ubeskyttet.
Læring
En almindelig fejl i årsagsanalyse er at samle alle relevante kompetencer, som elektricitet, mekanik og automatisering, i ét rum. I sådanne tilfælde bestemmer man ofte på forhånd, at årsagen skal findes på det møde, hvilket ofte viser sig at være umuligt.
Hvad der sker, er, at holdet går rundt og håber, at den person, der har de rette færdigheder, også kender årsagen til problemet. Denne person vil ofte komme med en teori om rodårsagen, men der er stor risiko for, at en forkert teori bliver anerkendt som sandhed. Det er vigtigt at huske, at sandheden ikke findes i mødelokalet, men derimod i processen.
I stedet bør alle relevante kompetencer samles til et specifikt tidspunkt for intens brainstorming. Fokuser ikke på, hvad der virker sandsynligt eller ej, men på at generere så mange teorier som muligt. Efterfølgende vurderes teorierne og gives point baseret på deres sandsynlighed. Den teori med den højeste score går videre til testfasen.
Test, test, test
Lad årsagsanalysen tage den nødvendige tid. Tag din teori og gå ud i virkeligheden for at teste, om den holder. Interview de relevante personer, såsom operatører, automationsteknikere og maskinleverandører. Disse fagfolk kan fortælle, hvad der sker, eller hvordan fejlen bør undersøges, men de kan ikke nødvendigvis forklare, hvad fejlen afhænger af. Når den første årsag er blevet bekræftet som sand, kan du formulere det næste „hvorfor‟ og fortsætte processen.
Data spiller en central rolle i en årsagsanalyse. Hvis en teori er, at problemet skyldes lavt tryk, og du har mulighed for at måle trykket og sammenligne den faktiske værdi med setpunktet, kan du hurtigt adskille spekulationer fra fakta.
Nogle gange kan det være hurtigt at teste en hypotese, mens det andre gange kan tage flere måneder. En af de mest almindelige fejl med „5 hvorfor‟-metoden er at have for travlt og ikke teste hypoteserne grundigt nok.
Forholdet mellem årsag og virkning
Sildebensdiagrammet, også kaldet Ishikawa-diagrammet, er en metode til at visualisere forholdet mellem årsag og virkning, hvilket hjælper med at belyse hovedproblemet. Navnet stammer fra Kaoru Ishikawa, der opnåede stor succes med metoden på Kawasaki-værftet i 1960’erne.
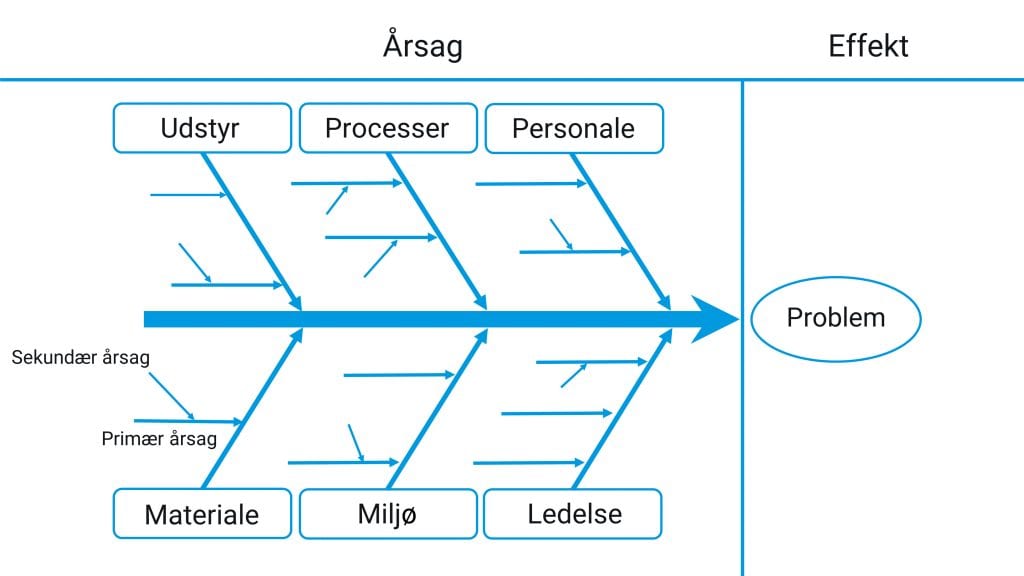
Årsagsanalyse i kombination med Ishikawa diagrammet
Sildebensdiagrammer er ikke velegnede til alle typer problemer. De er mest nyttige, når problemet er komplekst. Diagrammet bør ikke bruges alene, men i kombination med brainstorming eller andre metoder til idéindsamling sammen med 5 gange hvorfor.
En årsagsanalyse, der kombinerer et Ishikawa-diagram, kan se sådan ud:
- Brainstorming: Indsamling af mulige årsager.
- Sildebensdiagram: Placering af de idéer, der er genereret under brainstormingen, i diagrammet og overveje, hvilke der kan være relaterede. En årsag kan være en konsekvens af en anden.
- Multioption: Valg af den mest sandsynlige teori.
- 5 gange hvorfor: Gennemgang af teorien for at verificere, om den er korrekt, og identificere årsagen til problemet. Revidering eller tilføjelse af flere underliggende niveauer og deres relationer til sildebensdiagrammet. 5 gange hvorfor kan føre til en omlægning af sildebensdiagrammet.
- Brainstorming: Indsamling af ideer til løsninger.
- Multival: Valg af løsninger, der sandsynligvis vil have størst effekt på kort tid og til lavest mulig omkostning.
- Opfølgning: Sikring af, at løsningen har haft den ønskede effekt.
Derfor er årsagsanalyse vigtigt for produktionsvirksomheder
At identificere årsager til produktionsproblemer giver store fordele. Maskinleverandører har ofte ekspertise i maskiner, men kender ikke altid produktet i praksis. Faktorer som materialer, miljø og rutiner spiller en vigtig rolle og kræver en grundig gennemgang af operationen. Den egentlige årsag findes ofte gennem gentagne tests.
Komplekse problemer kræver mere end et enkelt møde, mens enklere udfordringer kan løses med metoder som „5 gange hvorfor‟ og interviews. Manglende viden, information eller fakta er ofte kerneproblemet. Værktøjer hjælper med at udvikle symptomløserne til problemløsere – og på sigt til problemforebyggere.
Det er ikke ualmindeligt, at nogen i gruppen gætter rigtigt tidligt, men årsagsanalysen sikrer, at hele teamet får den samme forståelse og enes om løsninger. Det afgørende er ikke, hvem der havde ret, men at problemet bliver løst.